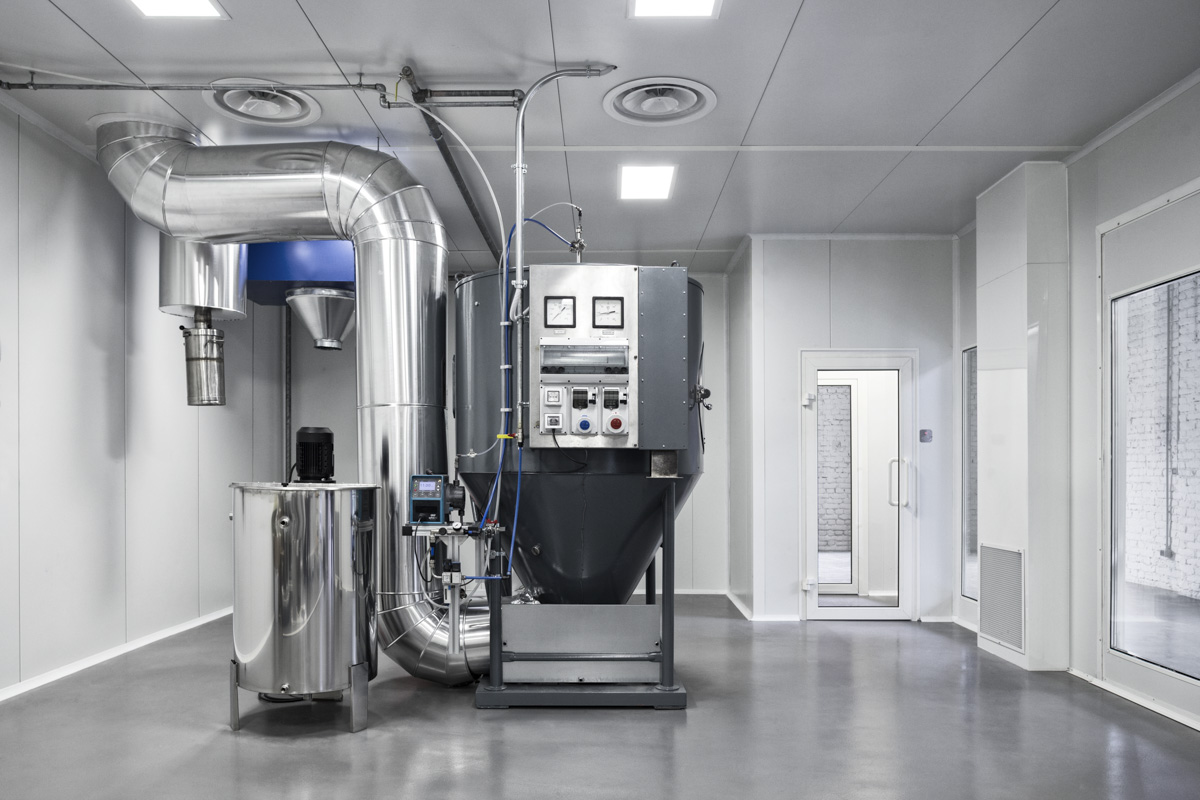
ItaliaOggi
18/08/2020
BY FILIPPO MERLI
An eco-friendly asphalt. Made with a mixture that starts from a plastic recovery process based on the circular economy. The new material was conceived by Iterchimica, a Bergamo-based company that has been active since 1967 in the design and production of products that improve the performance of road surfaces. Like the one on the new bridge in Genoa. The project was born five years ago with the aim of recovering plastics that are not recycled, but that end up in the waste-to-energy cycle. The company in Bergamo has tested it on some particularly critical sections of the road, such as the airport runways of the Fiumicino airport. And a few months ago, it was chosen by Webuild, the group of the construction sector that together with Fincantieri has built the San Giorgio bridge, inaugurated last 3 August by the President of the Republic, Sergio Mattarella. The asphalt used for the former Morandi bridge resists twice as long as traditional asphalt. Inside there are recycled plastics and graphene, which give the asphalt a resistance greater than 250% compared to normal. Inside the asphalt, the plastics of the toys or those of benches are recovered. Materials that prior to this patent were not part of the recycling chain. “Our company has two patents on this product,” explained Federica Giannattasio, CEO of Iterchimica. “The first for the plastics recovery process and the second for the final additive that is made”. The company based in Suisio, a centre of about 3,800 inhabitants in the province of Bergamo, has another production unit in Carvico and two subsidiaries abroad. It operates in 80 countries. Among the most significant international projects is that of Doha airport, in Qatar, where Iterchimica has built the take-off and landing runway. Then there’s Italy. And Genoa. The place where Iterchimica, to create the asphalt of the new viaduct, involved Diretta Plus, a Como-based graphene company, and G.Eco, a company from the Brescia multiutility A2A that supplied the component of hard plastics for recovery. At the headquarters of the Bergamo group, chemists and engineers worked in parallel: the first on materials, the second on design. Subsequently, the asphalt mixture was developed by the official Poliedro laboratory. “Once the right mixture was developed,” Giannattasio stressed, “we accompanied the company responsible for laying the asphalt to the construction site. Those were weeks of hard work, lived at a very intense pace, but for the company and for our team, it was a great satisfaction. Experiencing that construction site, taking part in the construction of such a significant work, has been exciting and a source of pride for a company like ours, which focuses everything on innovation and research”.
-Reproduction reserved-